INNOVATION STORIES
PRODUCTION PRINT
Going back to the roots of production print
History of innovative proposals that changed the conventional wisdom of the printing industry
- INDEX
You may be surprised to know that printing, along with photography, has been one of Konica Minolta’s businesses since its founding. In fact, when the company was founded 150 years ago, we imported and sold materials and tools for lithography, which was the origin of the development of printing in Japan. We maintained business ties with printing companies while expanding our photographic film and X-ray film businesses. In the 1970s, we started to develop and manufacture printing films, which were used for offset printing (analog printing), and delivered the films to printing worksites. We have been deeply involved in the printing industry for many years.
Based on our close ties with the printing industry, our current production print business offers technical support and consulting in addition to products and services. With printing methods expected to shift gradually from analog to digital, production print focusing on digital printing is one of our growth domains.
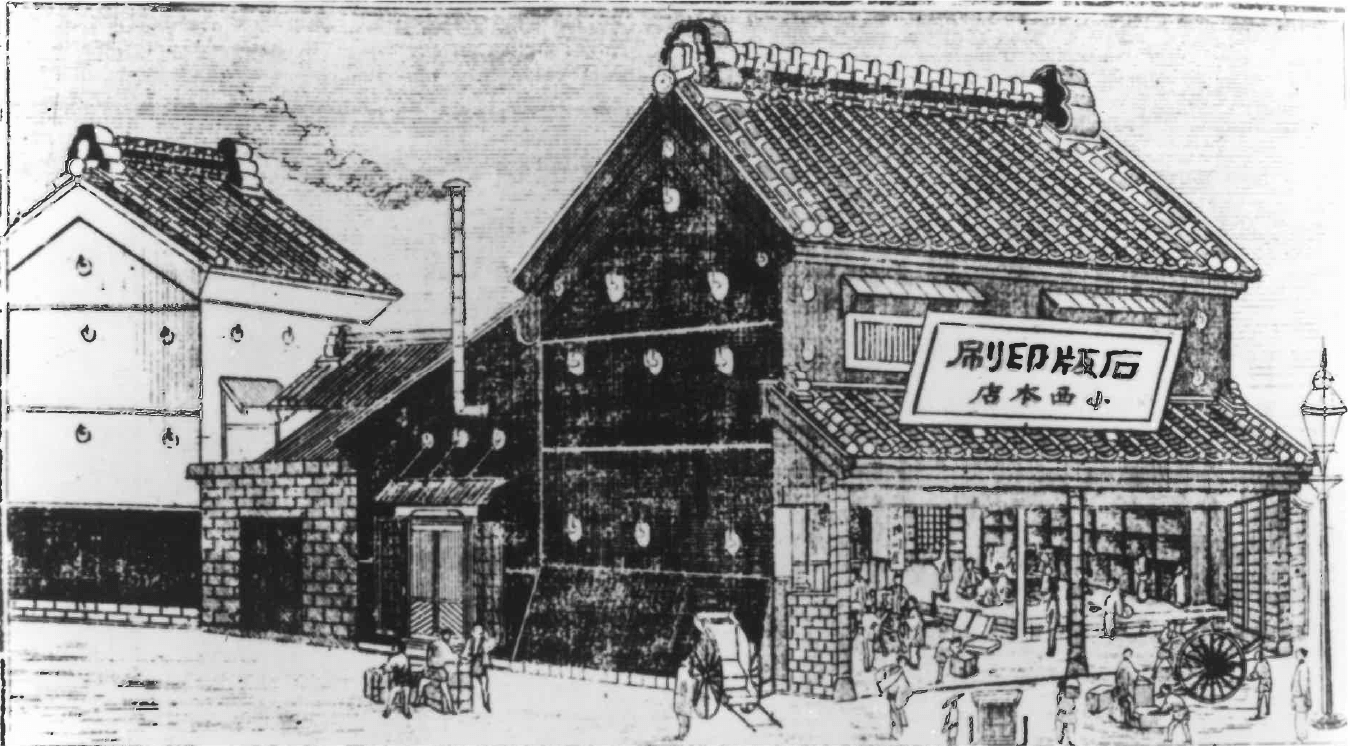
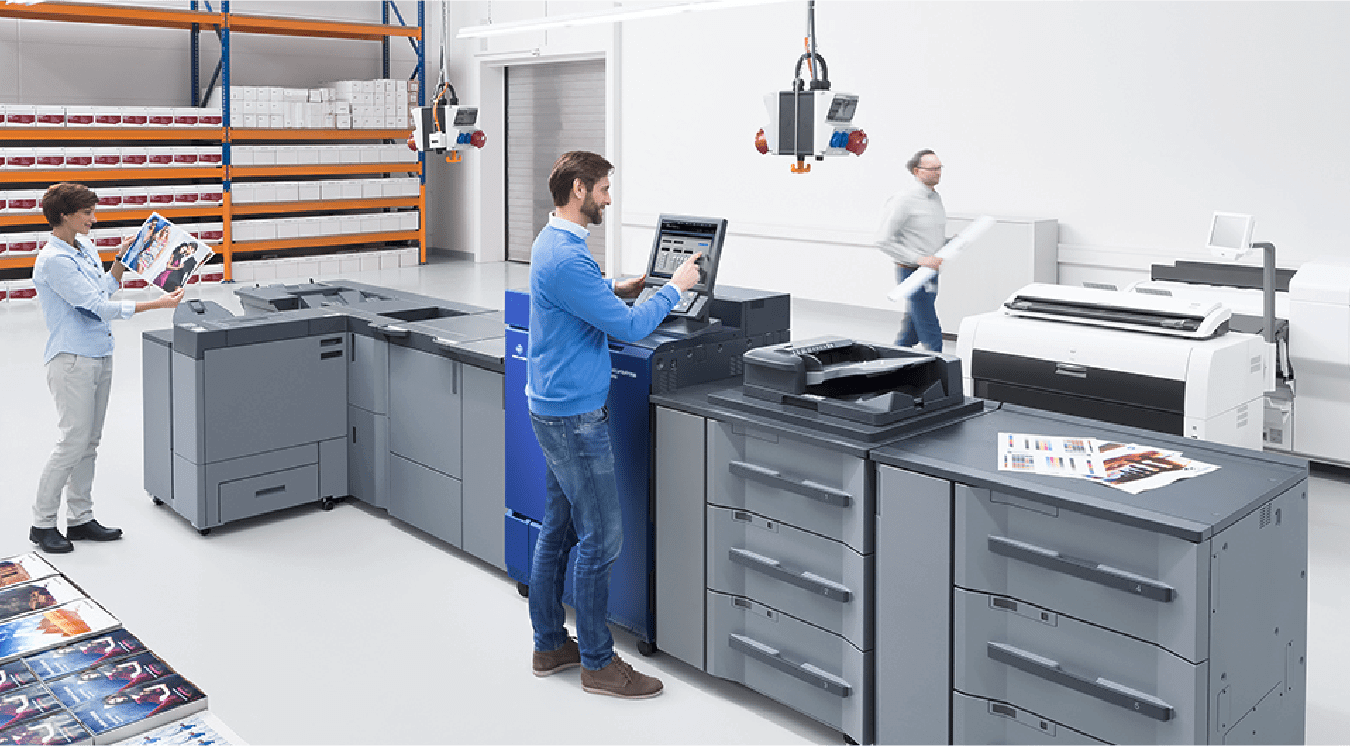
Reason why “konse” was used as a verb for color proofing in Japan
Konsensus, a simple color-proofing system released by Konica in 1987, is a landmark product in the history of our business.
Color proofing refers to the process of performing test printing before actual printing, to check that the colors are reproduced as designated. At that time, color proofing was performed by using machines for actual printing or those dedicated for color proofing (flat-bed color-proofing machines) and actual printing plates. However, this was a time-consuming and labor-intensive process, and it was difficult to reproduce the same colors as those of actual printing. The process required highly skilled workers. Furthermore, it was impossible to print only one or two copies - so there were some materials wasted, where only a small number of copies were needed.
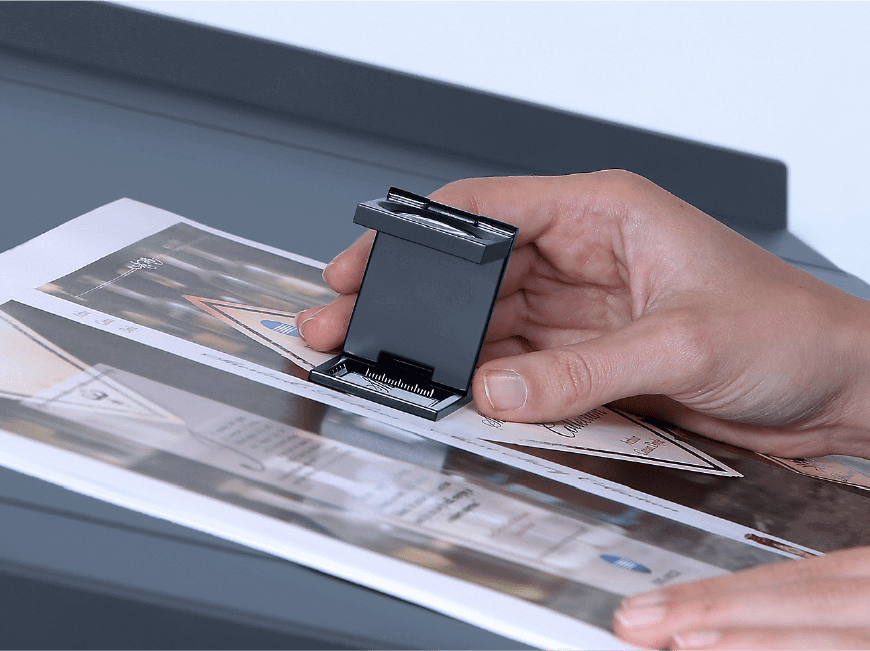
Is it possible to output color-proofing paper more easily? One of the technical issues was to properly reproduce halftone dots, which determine the contrast of images, close to actual printing. If reproduction is inadequate, even if the results of color proofing appear to be good, halftone dots may overlap and generate stripe patterns called moiré due to interference when printing is performed using machines for actual printing. Inadequate reproduction also makes it difficult to determine the quality of photographic details.
Is there a technology to properly reproduce halftone dots? The development team focused on silver halide color photography, an in-house technology refined through many years of operations. Although the technical hurdle to attain image quality close to that of printing was very high, the development team completed the Konsensus, a revolutionary simple color-proofing system capable of quickly outputting color proofs. The team came up with innovative, unique ideas and made improvements to enhance the image quality of printed matter based on silver halide color photography. The running cost was also greatly reduced.
This simple color-proofing system was highly evaluated in the global market and was an instant hit in the printing industry. Indeed, in Japan, it became so widely accepted in the printing industry and among its customer, the publishing industry, that the word “konse” came to be used as a verb, which meant to perform color proofing.
At that time, it was the dawn of digital printing era. When the printing and printmaking film business started to lose momentum, the evolution continued, from analog Konsensus, which used printing and printmaking films, to digital Konsensus, which directly performed laser exposure based on the printing data. Thus, Konsensus helped maintain the ties with the printing industry.
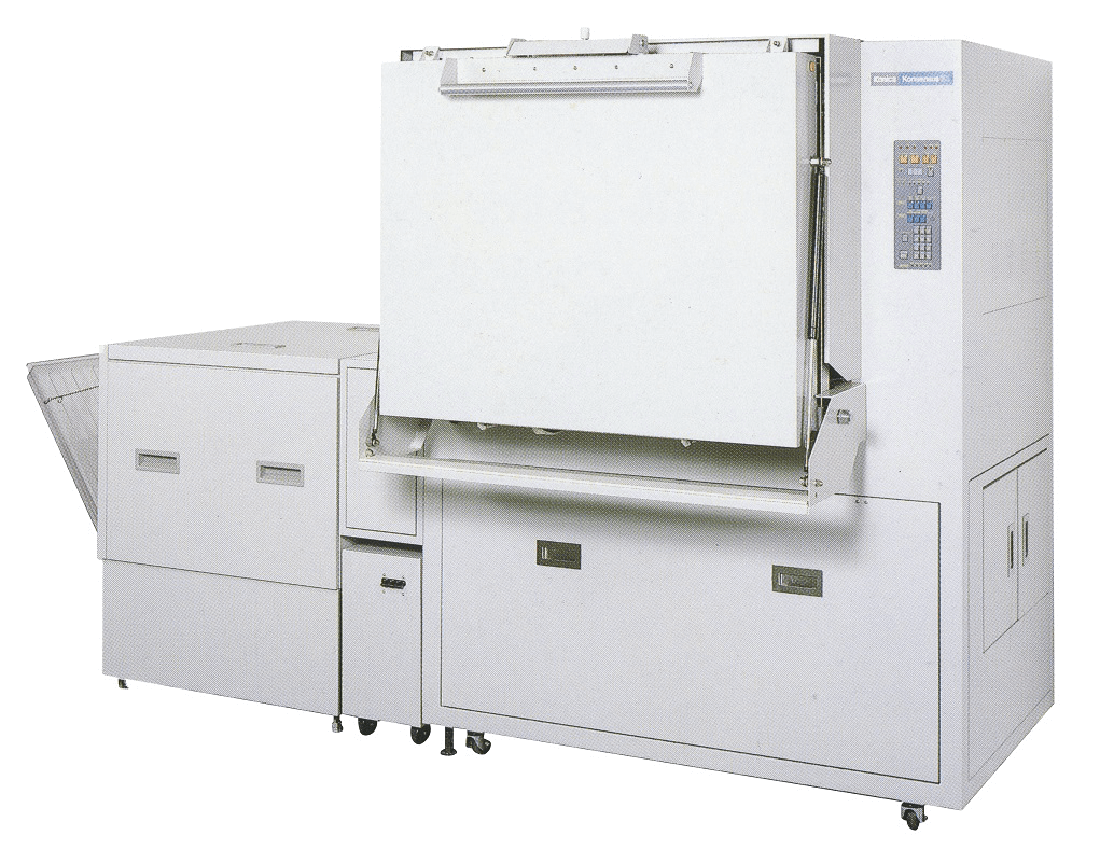
Positive feedback from printing companies: “This is useful!
Another key product in our history is the high-speed digital color MFP 8050, which was released in 2003 based on our strong ties with the printing industry and color copier technology, which was refined in the 1990s. This was our first hit product after serious consideration to shift to digital printing. The product received positive feedback about its usefulness from printing companies, which had previously avoided digital printing.
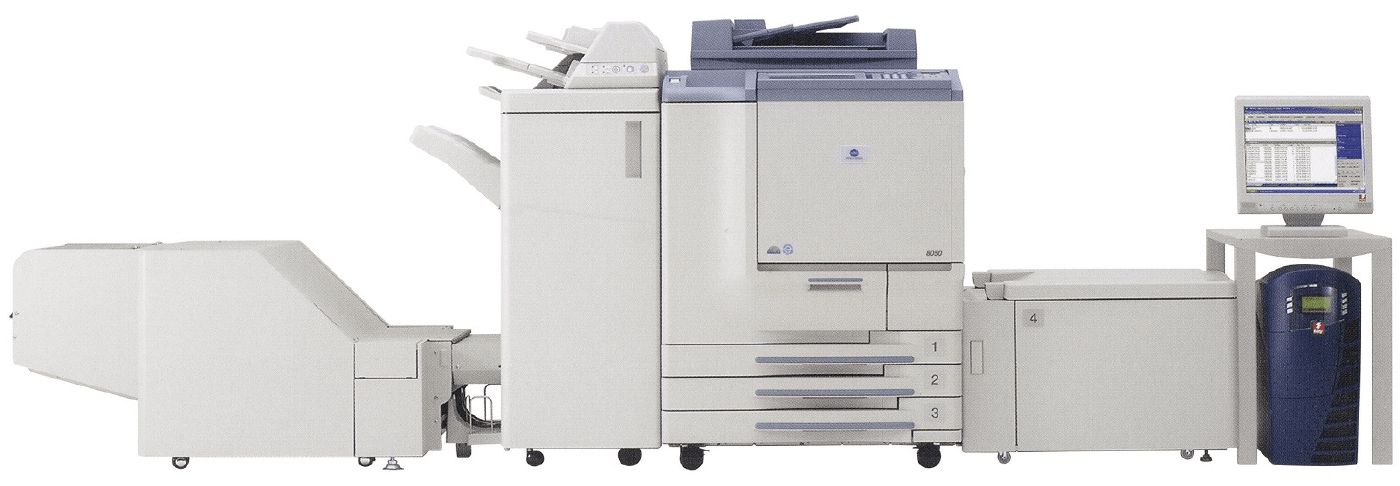
In the development project, sales staff members who knew the printing industry well set the development target, and copier engineers then worked toward it. They mainly focused on the printing speed, quality, and ability to use various types of paper, striving to achieve with digital technologies what was possible with analog. Price was another crucial factor for customers; the price had to be kept as low as possible while raising performance.
Sometimes, development engineers faced seemingly impossible requests they felt were unreasonable. One example was a request to use coated paper, which is paper coated with an agent on its surface, as printing paper.
Pulverized toner, which was mainly used at that time, had to be heated to 190°C in order to be fixed on paper. However, applying such intense heat to coated paper would generate bubbles due to the evaporating moisture becoming trapped under the coating agent on the surface.
A breakthrough was made by using polymerized toner, which had been under development from around 1990. Unlike conventional toner, which was manufactured by pulverizing large chunks of toner compounds, polymerized toner was chemically synthesized to achieve fine and uniform particles and significantly enhance the image quality of printed matter. It did not require the application of intense heat because it melted at a lower temperature than pulverized toner. Thus, polymerized toner opened the door to digital printing.
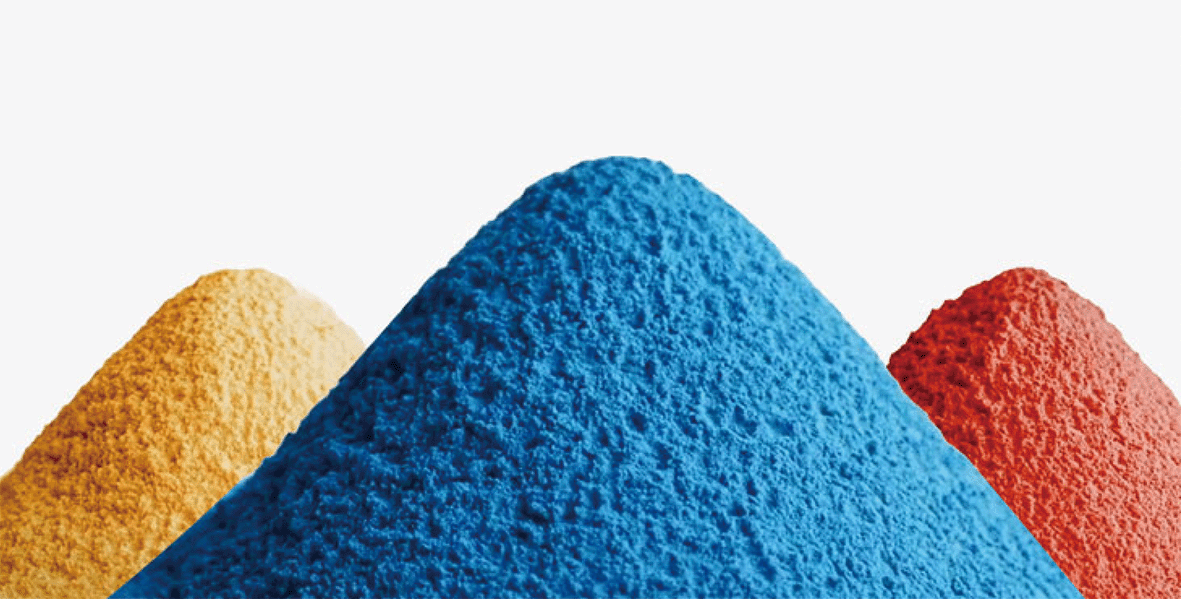
The high-speed digital color MFP 8050 was hugely successful and gained a reputation as the ideal way to introduce digital printing thanks to our efforts to strike a balance between performance and price. Even major companies in the industry were conducting trials to decide whether to go digital. For small printing companies, printing machines were too expensive and unaffordable. By releasing the 8050, we made a breakthrough and the digital printing market more than doubled, quickly.
Why did we aim to improve the workflow of printing worksites?
In 2007, Konica Minolta exited the printing film business and started to focus all of its resources on digital printing. However, our ties with the printing industry remained strong, and so we harnessed this strength.
The symbolic product was the Intelligent Quality Optimizer IQ-501, an automatic quality optimization unit released in 2017.
This unit automated the management of density and tone and the adjustment of position for duplex printing, which were labor-intensive processes and required highly skilled workers at printing worksites, by using proprietary technologies. For the development, we considered how to improve the workflow and enhance the processing capacity of printing companies. The concept was completely different from that of conventional product development, which prioritized cost-performance. This marked a major turning point in our product and system development.
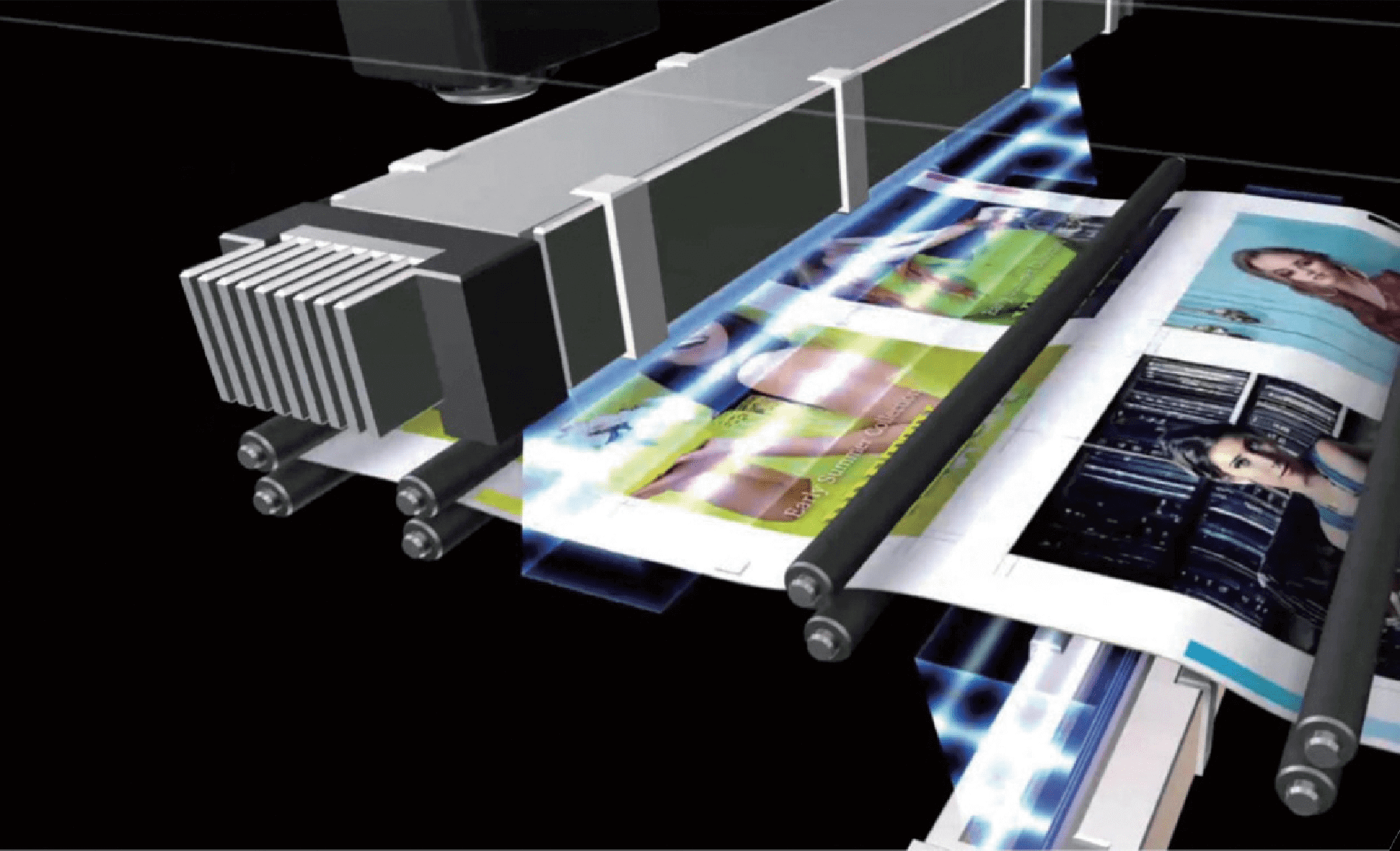
How did we succeed in changing our concept quickly, when most digital printer manufacturers were still developing products that aimed to improve printer performance?
The story dates back about five years before. At that time, digital printing systems were spreading more slowly than expected. After some analysis, we concluded that digital printing was unprofitable for printing companies.
At printing worksites, work that required human intervention from receiving to shipping an order had 65 steps on average. However, customers were billed only for the printing and binding processes, which accounted for about 10% or 20% of the entire process. In addition, there was a lot of work which could not be billed, such as rework and disposal caused by mis-operation. Nevertheless, analog printing companies, which received bulk orders, were able to absorb the costs in their overall revenue. However, this is not true for digital printing companies which accept orders for small lots per order.
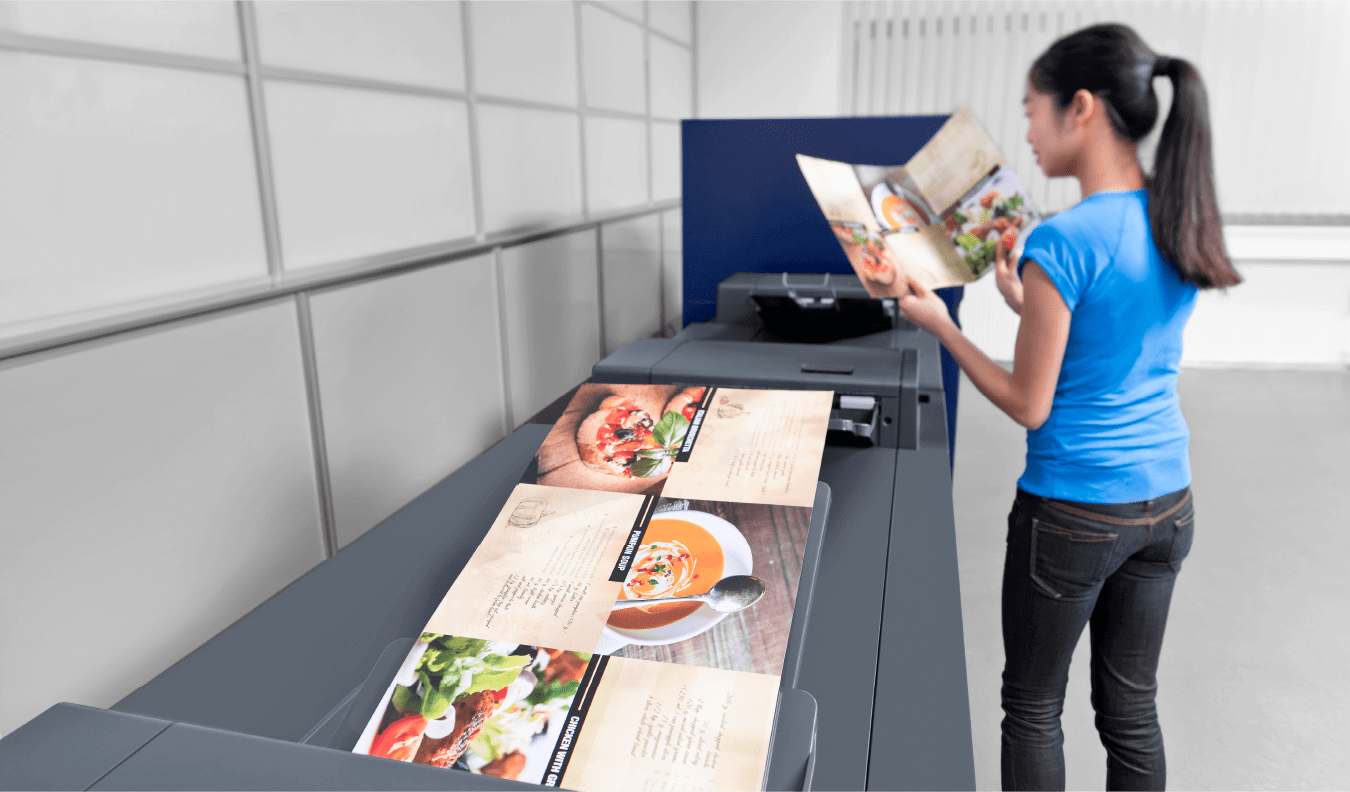
We decided to help printing worksites reduce their non-printing work and increase their profit by digital printing. That required automating the upstream and downstream processes of printing, which were time-consuming for operators. We focused on reducing the work time and thereby reducing the downtime of printing machines. We were able to overturn the norms of printing companies by carefully analyzing customers’ sites and accurately identifying their problems.
Automation of tone management was made possible by our proprietary sensing technology to measure the colors of light and objects. This technology, which was derived from Minolta’s superb photometry, was highly evaluated in the global market. In 1967, we developed the Minolta Space Meter, an exposure meter to be used in space, at the request of the National Aeronautics and Space Administration (NASA). The development of the automatic quality optimization unit demonstrated the synergies of our in-house engineering capabilities.
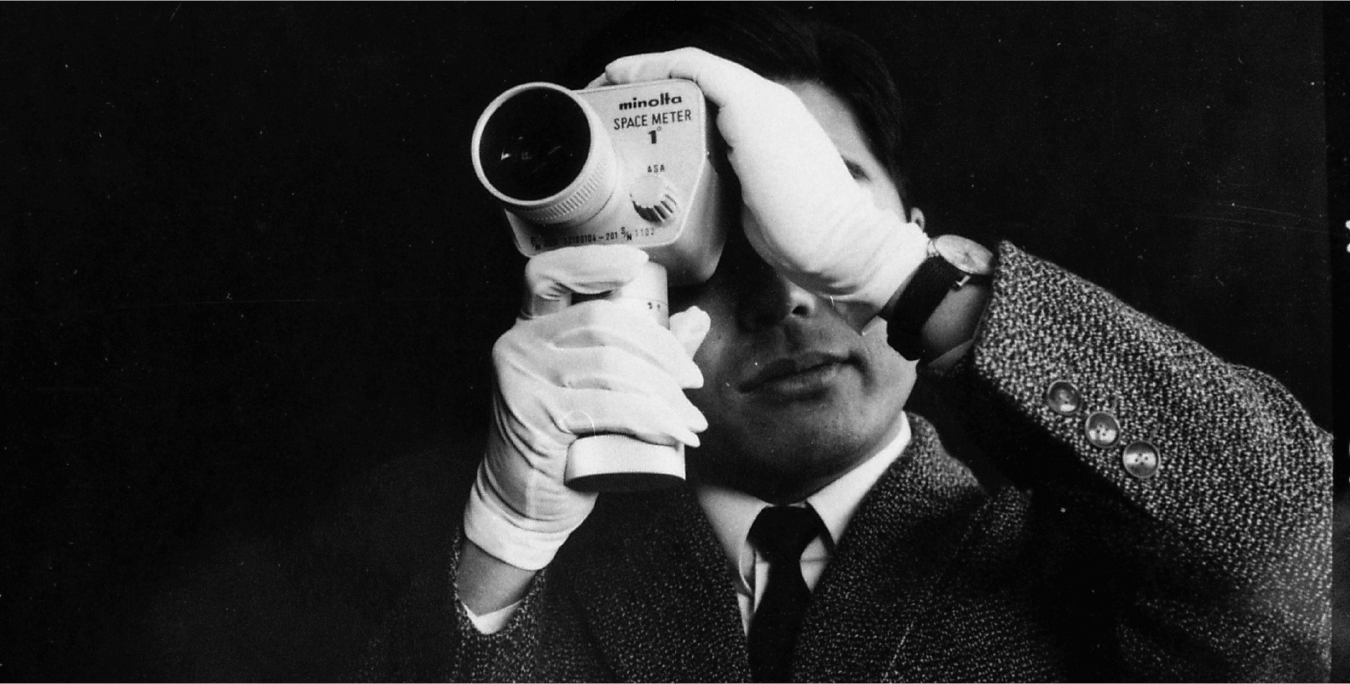
This novel concept, focusing on the workflow at printing worksites, was popular with customers. Today, the IQ-501 has a well-established reputation in the printing industry.
In the printing industry, the number of skilled operators has been decreasing, making it essential to automate the labor-intensive tasks and those that require expertise and achieve uniform printing quality. In tandem with the growing shift from analog to digital, the production print business must address such challenges faced by customers.
Today, companies are expected to take environmental measures to address climate change and ensure the effective use of limited resources. Digital printing offers the advantage of printing on demand, which certainly leads to a reduction in environmental impact. The quantity of materials used can also be reduced compared to analog printing because no printing plate is required. This environmental contribution is an important duty of the production print business. We remain committed to working closely with customers.
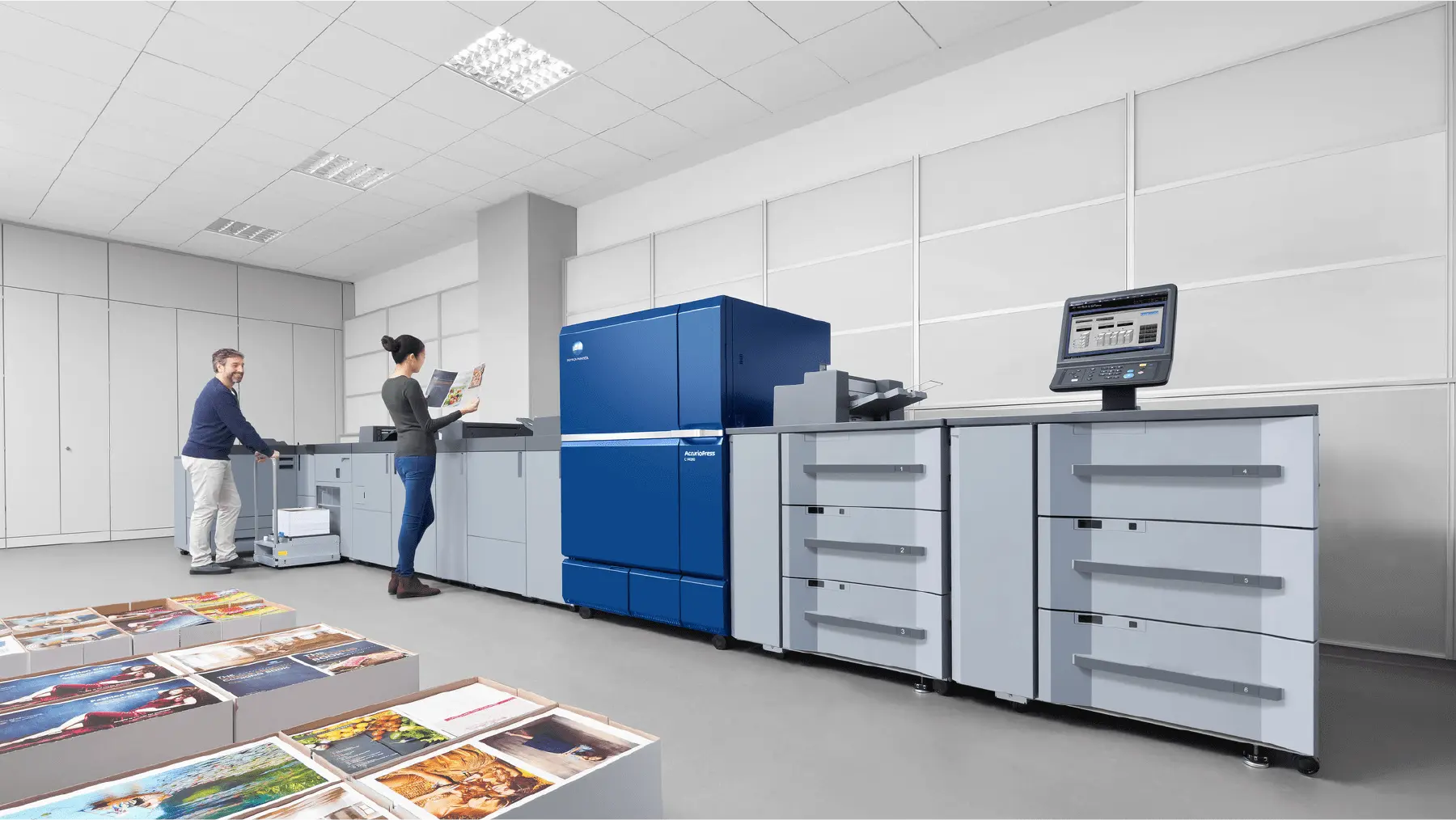
In the interest of clarity, “Konica” and “Minolta,”—the trade names that were used before the merger that formed “Konica Minolta”—are used throughout this text. Each company underwent a number of name changes throughout their history.
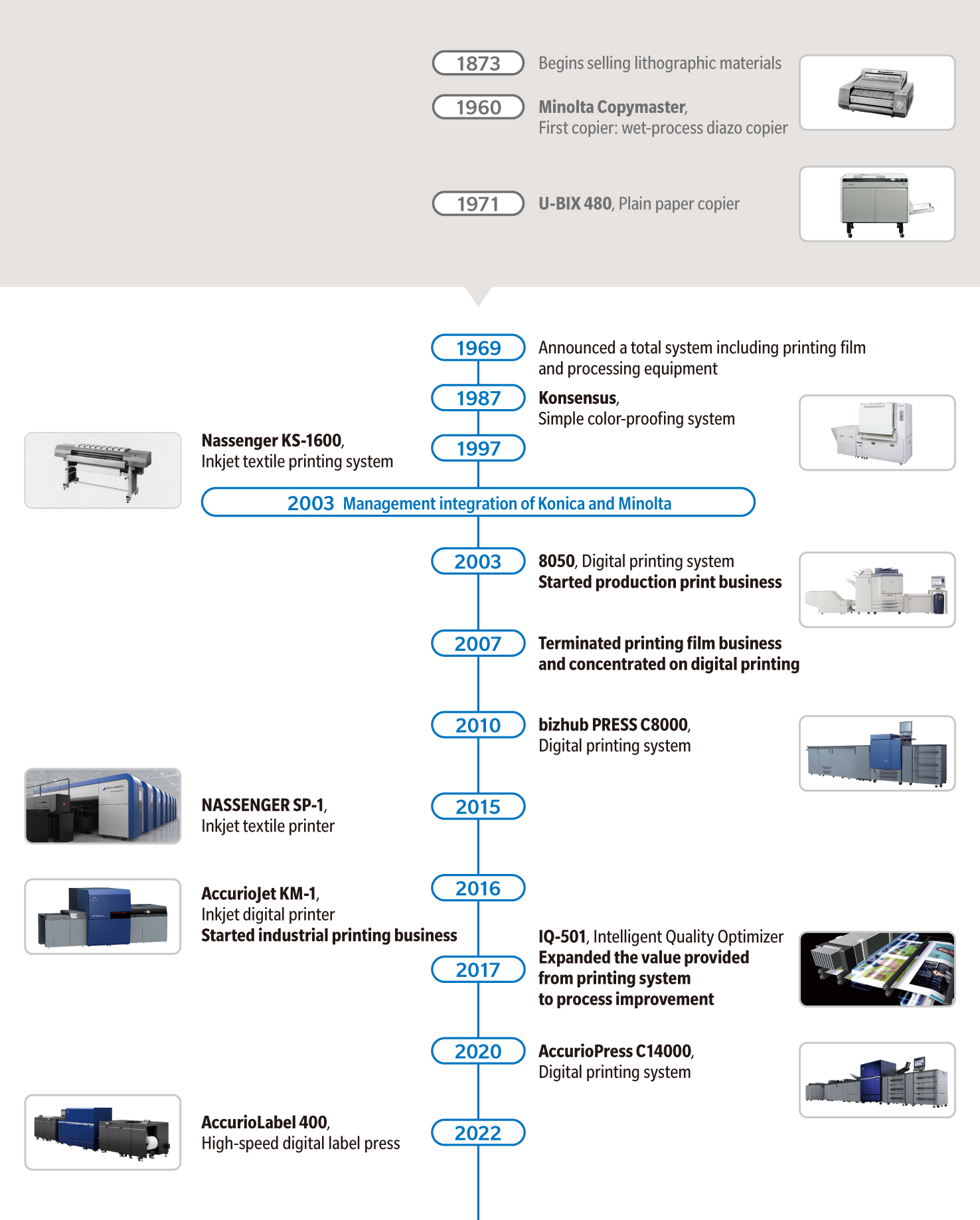