Prisms
Konica Minolta develops and manufactures glass prisms backed by our proven track record and plastic prisms that can be freely shaped and that are lightweight.
Examples of products we offer
Glass-Polished Prisms
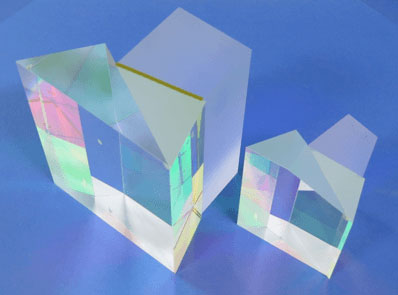
Prism unit products capable of optical path modification, and color separation and combination
Glass prism units for high-precision and high-luminance used by digital cinema (movie theater) projector manufacturers. These products are used to color-separate a white light source into three primary colors or to combine the projected light of three primary color images into the same light path. Konica Minolta not only has manufacturing technologies, such as glass polishing, coating, bonding, and installation of mechanical parts, but also various design technologies, such as stray light analysis and chromaticity value calculation, and can provide specialized designs for image display devices and light sources.
Product Specifications/Production Results
Mass production record: We have shipped a large number of dichroic prisms for projectors for more than 20 years since the dawn of digitalization of movies.
Size: Up to 135 mm in height and 100 mm in width
Surface accuracy: Newton ±1.5 fringe lines, Irregularity ±0.5 fringe lines
Plastic Prisms
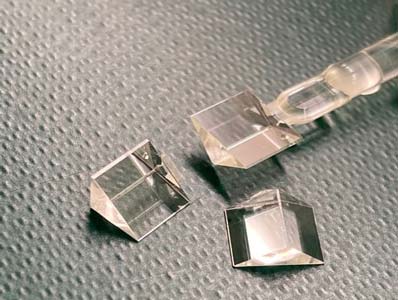
Shape flexibility and lightness made possible by plastic molding
Shape can be given to various applications by taking advantage of the shape flexibility of plastics (e.g., flanges for handling, positioning shapes, etc.).
Since it is possible to reduce the weight of prisms compared to glass prisms, please consider applying to products whose weight you want to reduce.
We also offer polygonal prisms and prism arrays.
Manufacturing Results
Product size: 1 to 20 mm
Surface accuracy (pv): 150 nm or less
Angular accuracy: 2’ or less
DOE Collimators
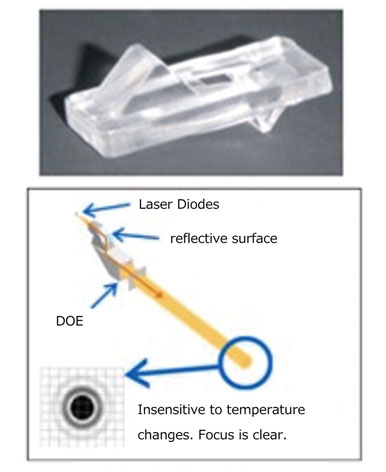
Laser Light Shaping Elements
One application of resin prisms is the DOE collimators used in laser printers, which integrate a lens and mirror. The laser beam emitted from the laser diode is collimated by the collimator lens, and then focused by the cylinder lens in the sub-scanning direction near the reflective surface of the polygon mirror. Conventionally, glass aspherical lenses are generally used for these lenses, but it is possible to create elements with a single resin component that can reduce lens and assembly costs. The two free-form surfaces of the two reflective surfaces and the incident and emitted surfaces are diffractive surfaces, which minimize aberrations and suppress temperature-related performance changes.
For more information
For inquiries and document downloads, please click here.
Click here to contact us
Click here to download the document